*TM 1-1500-204-23-5
Change 3
1-5/(1-6 blank)
Mechanical advantage is the ratio between the
resistance and the effort applied to a lever. This is ex-
pressed in the following formula:
Proper use of mechanical advantage enables a
relatively small force to overcome a larger resisting force
by applying the effort through a longer distance than the
resistance is moved. For example, to lift a 4--pound
weight (R) which is 2 inches from the fulcrum of a Type
1 lever requires 1 pound of effort (E) applied 8 inches
from the fulcrum. The mechanical advantage of this lever
would be as follows:
Thus, the applied effort in the example would
move through a distance that is four times greater than
the distance the resistance would move.
(2)
Moment of Force. A moment of force is the
product of a force or weight and a distance. To find a
levers moment of force, multiply the applied effort by the
distance between the point of effort application and the
pivot point (fulcrum). If the moment of force of the applied
effort equals the moment of force of the resistance, the
lever will balance. If an object to be balanced on a Type
1 lever weighs 4 pounds and is located 2 inches from the
fulcrum, it could be balanced by a 2--pound effort applied
4 inches from the fulcrum on the opposite side or by a
1--pound effort applied 8 inches from the fulcrum.
g.
Vibration. Any type of machine vibrates. Howev-
er, greater than normal vibration usually means that there
is a malfunction. Malfunctions can be caused by worn
bearings, out--of--balance conditions, or loose hardware.
If allowed to continue unchecked, vibrations can cause
material failure or machine destruction. Aircraft -- particu-
larly helicopters -- have a high vibration level due to their
many moving parts. Designers have been forced to use
many different dampening and counteracting methods to
keep vibrations at acceptable levels. Some examples
are:
D Driving secondary parts at different speeds to
reduce harmonic vibrations; this method removes
much of the vibration buildup.
D Mounting high--level vibration parts such as drive
shafting on shock--absorbent mounts.
D Installing vibration absorbers in high--level vibra-
tion areas of the airframe.
(1)
Lateral. Lateral vibrations are evident in
side--to--side swinging rhythms. An out--of--balance rotor
blade causes this type of vibration. Lateral vibrations in
helicopter rotor systems are quite common.
(2)
Vertical. Vertical vibrations are evident in
up--and--down movement that produces a thumping ef-
fect. An out--of--track rotor blade causes this type vibra-
tion.
(3)
High--Frequency. High--frequency
vibra-
tions are evident in buzzing and a numbing effect on the
feet and fingers of crew members. High--frequency vibra-
tions are caused by an out--of--balance condition or a
high--speed, moving part that has been torqued incor-
rectly. The balancing of high--speed parts is very impor-
tant. Any build--up of dirt, grease, or fluid on or inside
such a part (drive shafting, for example) causes a high--
frequency vibration. This type vibration is more danger-
ous than a lateral or vertical one because it causes crys-
tallization of metal, which weakens it. This vibration must
be corrected before the equipment can be operated.
(4)
Ground Resonance. Ground resonance is
the most dangerous and destructive of the vibrations
discussed here. Ground resonance can destroy a heli-
copter in a matter of seconds. It is present in helicopters
with articulated rotor heads. Ground resonance occurs
while the helicopter is on the ground with rotors turning;
it will not happen in flight. Ground resonance results
when unbalanced forces in the rotor system cause the
helicopter to rock on the landing gear at or near its natural
frequency. Correcting this problem is difficult because
the natural frequency of the helicopter changes as lift is
applied to the rotors. With all parts working properly, the
design of the helicopter landing gear, shock struts, and
rotor blade lag dampeners will prevent the resonance
building up to dangerous levels. Improper adjustment of
the landing gear shock struts, incorrect tire pressure, and
defective rotor blade lag dampeners may cause ground
resonance. The quickest way to remove ground reso-
nance is to hover the helicopter clear of the ground.
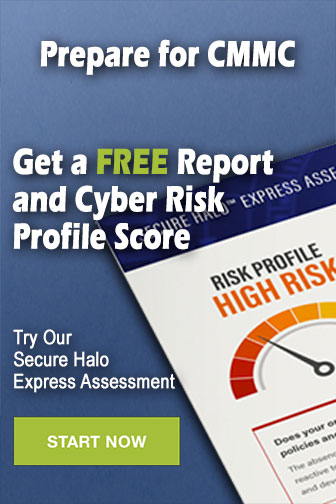