TM 1-1500-204-23-5
(1) General inspection. Propellers must be
inspected regularly. The exact time interval for particular
propeller inspections is usually specified by the propeller
manufacturer. The regular daily inspection of propellers
varies little from one type to another. Typically it is a
visual inspection of propeller blades, hubs, controls, and
accessories for security, safety, and general condition.
Visual inspection of the blades does not mean a careless
or casual observation. The inspection should be
meticulous enough to detect any flaw or defect that may
exist.
(2) Checking hub for looseness. Check to make
sure bolts are properly installed and tightened. If nuts can
be turned, remove cotter keys and retorque to required
setting.
(3) Checking blades for looseness. Check to see
that blades are properly installed in accordance with the
applicable maintenance manual.
(4) Checking external surfaces for metal propellers.
Metal propellers and blades are generally susceptible to
fatigue failure resulting from concentration of stresses at
the bottom of sharp nicks, cuts, and scratches. It is
especially
necessary,
therefore,
to
frequently
and
carefully inspect them for such injuries. Propeller
manufacturers have published service bulletins and
instructions which prescribe the manner in which these
inspections are to be accomplished.
(5) Checking propeller governor. Check propeller
governor for leakage, security of attachment, and general
condition. Inspect governor oil for metal particles.
(6) Inspection of a disassembled propeller. During
major overhaul, the propeller is disassembled, and all
parts are inspected and checked for size, tolerances, and
wear. A magnetic inspection or another type of
nondestructive test is usually made at this time to
determine whether any fatigue cracks have developed on
the steel components and assemblies.
(7) Local etching. Local etching is used to detect
cracks on propellers. Use the following procedures:
(a) Local etching shall be performed with a
solution locally prepared by adding one pound of sodium
hydroxide, technical, Federal Specification O-S-598, to
one gallon of water. Amount of solution to be prepared
will be determined by amount of etching to be performed.
(b) Clean and smooth area containing
apparent crack by sanding area with No. 00 sandpaper or
crocus cloth, Federal Specification P-C-458.
CAUTION
Do not allow sodium hydroxide or nitric
acid solution to contact blade thrust
washer. Damage to thrust washer may
otherwise result.
(c) Apply a small quantity of sodium
hydroxide solution mixed in accordance with para 2-9.c.
(7)(a) to suspected area with a small brush or swab.
CAUTION
Upon completion of etching, all traces of
sodium hydroxide shall be removed with a
solution
of
one
part
concentrated
technical grade propellant nitric acid,
Federal Specification O-N-350, to five parts
water. Wash blade thoroughly with clean,
fresh water. The blade shall then be dried
and anodized with chromic acid solution
in
accordance
with
MIL-A-8625
after
completion of all reworking. Damage to
propeller may otherwise result.
(d) After area is well darkened, thoroughly
wipe with a dampened cloth. When a crack extending
into metal exists, it will appear as a dark line or mark, and
by using a magnifying glass, small bubbles may be seen
forming in the line or mark
2-10. Propeller Repair. Repair propellers in accordance
with
the
best
accepted
practices
and
the
latest
techniques. Manufacturer recommendations shall be
followed. It is necessary to mark the name of the
manufacturer and model designation on the repaired
propeller in the event original markings were removed
during the repair or refinishing operations.
a. Minor Defects. Dents, cuts, scars, scratches,
nicks, etc., shall be removed or otherwise treated by
means of fine sandpaper and fine-cut files provided that
their removal or treatment does not materially weaken the
blade, materially reduce its weight, or materially impair its
performance or reduce the blade dimensions below the
minimums established by the manufacturer. Minimums
will usually be given in the manufacturer's service and
overhaul manual. The metal around longitudinal surface
cracks, narrow cuts, and shallow scratches shall be
removed to form shallow saucer-shaped depressions, as
shown in figure 2-3.
Change 2 2-9
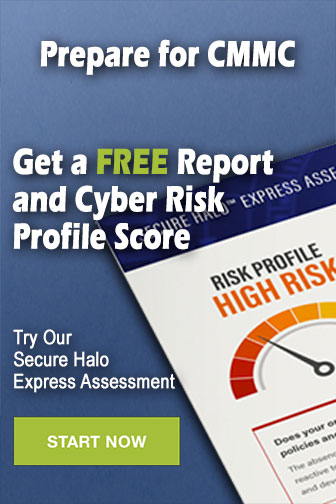