CHAPTER 1 - INTRODUCTIONCHAPTER 2 - COMPOSITE MATERIAL FACILITY OPERATIONSHAZARDOUS MATERIALSChronic ToxicityFigure 2-1. Carbon Fiber and Human Hair Diameters Compared to Filtration Level of HEPA FilterPERSONAL PROTECTIVE EQUIPMENT (PPE)Figure 2-2. Removing Disposable GlovesMATERIALS STORAGELaminating Resins and Paste Adhesives StorageEMERGENCY AND FIRST AID PROCEDURESCOMPOSITE REPAIR ENVIRONMENTSBONDING/LAYUP AREAFigure 2-3. Temperature and Humidity Allowables for Bonding and LayupTreatment AreaTable 2-1. - Personal Protective Equipment, Equipment/Facilities and Personal Hygiene for Working with Advanced Composite MaterialsTable 2-1. - Personal Protective Equipment, Equipment/Facilities and Personal Hygiene for Working with Advanced Composite Materials - ContinuedCHAPTER 3 - REPAIR EQUIPMENT, TOOLS AND SUPPLIESFigure 3-1. Alternating Tooth Bandsaw Blade for Cutting Aramid LaminatesHANDHELD TOOLSFigure 3-2. Heat Blanket ConigurationFigure 3-3. Welded Thermocouple WireFigure 3-4. Twisted Thermocouple WireAmbient TemperatureFigure 3-5. Heat Lamp Temperature Affects (Sheet 1 of 2)Figure 3-5. Heat Lamp Temperature Affects (Sheet 2 of 2)Figure 3-6. Double Vacuum Debulk (DVD Tool Schematic)Figure 3-7. Rigid Box ConstructionCONSUMABLE MATERIALSTable 3-2. - Material Temperature CapabilitiesTable 3-2. - Material Temperature Capabilities - ContinuedPatch and Fastener InstallationFigure 3-8. Blind Fastener DifferencesTable 3-3. - Mechanical FastenersFigure 3-9. Hi-Lok Installation: Hand ToolingFigure 3-11. Blind Fastener Grip Length Gauges (Sheet 1 of 2)Figure 3-11. Blind Fastener Grip Length GaugesBlind Fastener Inspection (Sheet 2 of 2)Table 3-5. - Composi-Lok II and IIa Installation ToolingTable 3-6. - Visu-Lok Installation ToolingTable 3-7. - Visu-Lok II Installation ToolingFigure 3-12. Typical Drill ReamerFigure 3-15. Spade Drill for Aramid LaminatesFigure 3-16. Brad Point Bit for Aramid or Fiberglass LaminatesFigure 3-18. Split Helix Router Bit for Trimming Aramid CompositesFigure 3-19. Countersink for Aramid LaminatesFigure 3-20. Coated Abrasive DiscFigure 3-21. Hole Saw and Guide BushingFigure 3-22. Honeycomb Core CuttersFigure 3-23. Industrial Hypodermic Syringe and NeedlesFigure 3-25. Vacuum CupFigure 3-26. Moisture IndicatorCoolantCHAPTER 4 - COMPOSITE MATERIALSFigure 4-2. Sandwich ConstructionFigure 4-3. Structural Property ComparisonPolyethyleneFigure 4-5. Warp vs. Fill Fibers in a Roll of FabricFigure 4-7. Twill Weave (2X2 Twill Shown)Figure 4-8. Satin Weave (4 & 8 Harness Satin Shown)Figure 4-9. Example Satin Weave Showing Alternating Warp and Fill Faces Used for LaminationFigure 4-10. BraidStitched Multiaxial FabricsFigure 4-11. Weave and Stitch ProcessFigure 4-12. Simultaneous Stitch ProcessRESIN TYPESSHELF LIFETable 4-2. - Shelf Life Data for Common Two-Part Epoxy AdhesivesADHESIVESFigure 4-13. Honeycomb Core Orientation and NomenclatureFigure 4-15. Overexpanded Honeycomb CoreCure In Place CoreLIGHTNING STRIKE PROTECTION, ELECTROMAGNETIC INTERFERENCE SHIELDING AND ELECTRICAL GROUNDINGCHAPTER 5 - TYPICAL DAMAGE AND ASSESSMENTTap TestingFigure 5-1. Inspection Tap Hammer DetailsNondestructive Inspection Method (NDI)Pulse-Echo Longitudinal Wave UltrasonicsFigure 5-2. Pulse-Echo Ultrasonic Inspection with A-Scan Presentation (Sheet 1 of 3)Figure 5-2. Pulse-Echo Ultrasonic Inspection with A-Scan Presentation (Sheet 2 of 3)Figure 5-2. Pulse-Echo Ultrasonic Inspection with A-Scan Presentation (Sheet 3 of 3)Figure 5-3. Through-Transmission Ultrasonic Inspection, A-Scan Presentation (Sheet 1 of 2)Figure 5-3. Through-Transmission Ultrasonic Inspection, A-Scan Presentation (Sheet 2 of 2)Figure 5-4. Types of DefectsHeat/Burn DamageDAMAGE ASSESSMENT METHODOLOGYFigure 5-5. Defect Mapping of Damage Extent from NDIFigure 5-6. Damage Work Lines Drawn on Part SurfaceFigure 5-7. Typical Orientation MarkingsFigure 5-8. Ply and Ply Fiber DirectionFigure 5-9. Fiber OrientationsFigure 5-11. Stacking Sequence EffectsFigure 5-12. Patch Drawing Example and Typical Scarf Repair Stackup (Sheet 1 of 2)Figure 5-13. Scab Patch Ply ArrangementFigure 5-14. Repair Ply Cutting Template (Example) (Sheet 1 of 3)Figure 5-14. Repair Ply Cutting Template (Example) (Sheet 3 of 3)Figure 5-15. ASTM Standard for Measuring Ply AnglesFigure 5-17. Example for Positive and Negative AnglesFigure 5-20. Example Odd Symmetric LaminateFigure 5-23. Example Sets for Non-Symmetric LaminatesFigure 5-24. Excerpt from CMH-17FFigure 6-1. Paint Removal ZonePAINT REMOVAL PROCEDUREFigure 6-2. Damage OutliningTable 6-1. - Ranking of Damaged Material Removal TechniquesFigure 6-3. Router Template FabricationFigure 6-4. Partial Thickness Damage RemovalFigure 6-5. Core Cell Axis OrientationFigure 6-6. Removal of Core With Core KnifeFigure 6-8. Typical Router Setup With TemplateCLEANING PROCESSWiping ProcessDRYING PROCESSFigure 6-9. Average Drying Time for Advanced Composite LaminatesHeat Blanket/Vacuum Technique.Removal of Water From Honeycomb CoreHeat Blanket, Oven or Hot Air Module MethodFigure 6-10. Patch Edge Taper DimensionsFigure 6-11. In-Plane Versus Out-Of-Plane Cutting ForcesFiberglassGeneral Air Tool SafetyPartial Thickness Damage RemovalKEVLAR-EPOXY REPAIRS PROCESSRemoval of Fuzzing by Back SandingFIBERGLASS-THERMOSETTING RESIN REPAIRSHONEYCOMB CORE REPAIR PROCESSFigure 6-12. Spoiling and Potting CoreFigure 6-13. Basic Repair JointsFigure 6-14. Basic Repair Joints (General)Figure 6-16. Basic Repair Joints (Bolted)Multiple Row Fastener PatternsFigure 6-17. Ply Overlap ChartFigure 6-18. Dimensions of a Scarf RepairFigure 6-20. Scarf Joint Outline LayoutFigure 6-21. Scarf Joint MachiningFigure 6-22. Laminate Fiber Orientation (Sheet 1 of 2)Figure 6-22. Laminate Fiber Orientation (Sheet 2 of 2)Figure 6-23. Scarf Joint Inspection RequirementsFigure 6-24. Step Joint Outline LayoutWET LAYUP METHODWET LAYUP METHOD - ContinuedWET LAYUP METHOD - ContinuedFigure 6-26. Ply Layup LogTools, Equipment, and Materials RequiredFigure 6-27. Vacuum Assist Impregnation Process (Sheet 1 of 2)Tools, Equipment, and Materials Required - ContinuedTools, Equipment, and Materials Required - ContinuedRESIN PREPARATION AND USEFigure 6-28. Two Part Adhesives and Filler Compounds FormulaFigure 6-29. Examples for Preparing Two Part Adhesives and Filler CompoundsTable 6-2. - Filler GuidelinesLiquid ShimmingVACUUM BAGGING THEORY AND TECHNIQUESFigure 6-30. Vacuum Bagging ArrangementTable 6-3. - Vacuum Pressure Conversion ChartSingle Side Vacuum Bag ProcedureEnvelope Bagging ProcedureFigure 6-31. Envelope Bagging a Part on a WorktableFacilities, Equipment, and MaterialsTwo-Side Access Seal TechniqueOne-Side Access Backside Seal TechniqueFigure 6-33. Component Sizes and Slotted Disc Geometry for Single-Side Access SealMethod 1, One-Side Access Backside Seal ProcedureFacilities, Equipment and MaterialsFacilities, Equipment and Materials - ContinuedVacuum Integrity TestSolving for Vacuum LeaksThermal Survey ConsiderationsFigure 6-35. Heat Blanket Placement and Temperature Variations in Repair AreaFigure 6-36. Typical Thermal Survey SetupCURING ADVANCED COMPOSITESFigure 6-37. Typical Cure CycleFigure 6-38. Typical Vacuum-Bagged Cure CycleCure TemperatureTable 6-4. - Maximum Cure Temperatures on AircraftPlacementFigure 6-39. Typical Thermocouple PlacementTemperature ControlHeat Blanket. Figure 6-40. Thermocouple Placement in Repair AreaHeat LampTable 6-5. - Typical Heat Lamp Performance ChartFigure 6-41. Pressure Levels Produced Using Various Pressure Methods (Sheet 1 of 4)Figure 6-41. Pressure Levels Produced Using Various Pressure Methods (Sheet 2 of 4)Figure 6-41. Pressure Levels Produced Using Various Pressure Methods (Sheet 3 of 4)Figure 6-41. Pressure Levels Produced Using Various Pressure Methods (Sheet 4 of 4)Figure 6-42. Methods for Applying Positive PressureFigure 6-43. C-Clamp Sequence and PlacementFigure 6-44. Typical Two Part Adhesive Heat Cure CycleTwo Part Adhesive Room Temperature Cure Cycle Method.Figure 6-45. Inspection of Adhesive Squeeze Out Following CureGALVANIC CORROSION OF CARBON COMPOSITES CHAPTER 7 - REPAIR PROCEDURESTable 7-1. - General Description of Different Repair Types Table 7-1. - General Description of Different Repair Types - ContinuedTable 7-1. - General Description of Different Repair Types - ContinuedTable 7-1. - General Description of Different Repair Types - ContinuedTable 7-1. - General Description of Different Repair Types - ContinuedFigure 7-1. Process Flow Diagram for Surface DamageFigure 7-2. Process Flow Diagram For Partial Thickness DamageBonded Repair Procedure.Figure 7-3. Partial Thickness Bonded RepairFigure 7-5. Layup of Stacked Patches and AdhesivePartial Thickness Scarf RepairPENETRATION DAMAGE REPAIRFigure 7-7. Process Flow Diagram for Penetration Damage RepairFull Thickness Scab RepairFull thickness Scab Repair Procedure.Figure 7-8. Cross Section of Typical Stepped RepairFull Thickness Step Repair Procedure.Moisture IngressionFigure 7-9. Core Replacement MethodsFigure 7-10. Replacement Core FitFigure 7-11. Weight Versus Hole Diameter for Two Core Replacement MethodsFigure 7-13. Procedure for Core Replacement Using the Core Potting MethodHoneycomb Core Repair Procedure.Figure 7-14. Process Flow Diagram for Core Repair, Paste Adhesive MethodPaste Adhesive Method Procedure.Paste Adhesive Method Procedure. - ContinuedFigure 7-15. Procedure for Core Replacement Using the Paste Adhesive MethodRapid DensiicationFigure 7-16. Process Flow Diagram for Rapid DensiicationAdhesive Bonded Joints Procedure.Figure 7-17. Layup of Stacked Patches and AdhesiveMECHANICALLY FASTENED JOINTSFigure 7-18. Basic Repair Joints (Bolted)Multiple Row Fastener PatternsTable 7-2. - Blind Fastener Inspection Requirements (VISU--LOK)Table 7-3. - Blind Fastener Inspection Requirements (COMPOSI-LOK)Figure 7-19. Hi-Lok RemovalFigure 7-20. Removal of Tightly Clamped Blind FastenersFigure 7-21. Removal of Loose Blind FastenersFigure 7-22. Hole FinderBlind Hole Transfer PunchesFigure 7-23. Blind Hole Transfer PunchFigure 7-24. Measuring and Scaling Method of Transferring Blind HolesFigure 7-25. Mold Method of Transferring Blind HolesMold MethodFigure 7-26. Arc Method of Locating Blind Fastener Holes (Sheet 1 of 3)Figure 7-26. Arc Method of Locating Blind Fastener Holes (Sheet 2 of 3)Figure 7-26. Arc Method of Locating Blind Fastener Holes (Sheet 3 of 3)Example Procedure For A Bolted Repair.Figure 7-27. Process Flow Diagram for Penetration Damage Bolted Repair, External PatchFigure 7-28. Sump Removal and InstallationFacilities, Equipment and Materials. Figure 7-29. Sealing Bolted RepairsFigure 7-30. Process Flow Diagram for Partial Thickness Bolted RepairPartial Thickness Bolted Repair ProcedureFigure 7-31. Types of DelaminationsFigure 7-32. Impact Damage Injection RepairFigure 7-34. Process Flow Diagram for Delamination Not Open to an Edge RepairResin Injection For Delaminations Not Open To An Edge Repair Procedure.Resin Injection For Delaminations Not Open To An Edge Repair Procedure. - ContinuedFigure 7-36. Delamination Repair Not Open to an Edge (Blister)Figure 7-37. Process Flow Diagram for Delamination Open to an Edge RepairFigure 7-38. Repair to an Open EdgeSkin to Core DisbondFigure 7-39. Process Flow Diagram for Disbond RepairFigure 7-40. Veriication of Leak Path: Disbond RepairFigure 7-41. Disbond RepairFigure 7-42. Process Flow Diagram for Skin to Closure MemberSkin to Closure Member Disbond and Delamination Procedure.Figure 7-43. Skin to Closure Member Disbond RepairEDGE DAMAGEFigure 7-44. Repair to an Open EdgeFigure 7-45. Process Flow Diagram for Edge Damage RebuildEdge Damage Rebuild Procedure.Figure 7-46. Process Flow Diagram for Flush Corner RepairFacilities, Equipment and MaterialFigure 7-47. Flush Corner Repair Sequence (Only Bonding on Upper Moldline is Shown for Clarity) (Sheet 1 of 2)Figure 7-48. Repair Rib Layup and ToolTrailing Edge Repair ProcedureTrailing Edge Repair Procedure - ContinuedTrailing Edge Repair Procedure - ContinuedTrailing Edge Repair Procedure - ContinuedTrailing Edge Repair Procedure - ContinuedFigure 7-49. Process Flow Diagram for Fastener RepairFigure 7-50. Process Flow Diagram for Countersink RepairFigure 7-51. Process Flow Diagram for Fill and Drill Fastener Hole RepairFigure 7-52. Template FabricationPotting MethodFigure 7-55. Potted Fastener Hole RepairPotting Fastener Hole Repair Procedure.Figure 7-56. Process Flow Diagram Fabric Layup RepairFigure 7-57. Fabric Layup Fastener Hole RepairFastener Hole Delamination RepairFigure 7-59. Vacuum Injection Fastener Hole RepairTable 7-5. - Clamp-Up Bolts and Torque Values 1Fastener Hole Delamination Repair ProcedureFigure 7-60. Application of Clamp-Up PressureFigure 7-61. Process Flow Diagram for Fastener Hole Repair: Swagged GrommetFigure 7-62. Swagged Grommet InstallFigure 7-63. Process Flow Diagram Captive Bushing RepairFigure 7-64. Captive Bushing Repair ComponentsFigure 7-65. Captive Bushing Repair Flange and Countersink Bushing InstallationFigure 7-66. Installation View of Captive Bushing RepairFacilities, Equipment and Materials. DVD Wet Layup Procedure.Table 7-6. - DVD ParametersDVD Wet Layup Procedure - ContinuedDVD Wet Layup Procedure - ContinuedDVD Wet Layup Procedure - ContinuedFigure 7-67. DVD Precure Stacking SequenceMethod 2: Cocuring to PartFigure 7-68. DVD Cocure Stacking Sequence (Typical)Locally Manufactured DVD ToolFigure 7-69. Double Vacuum Debulk Locally Manufactured ToolFigure 7-70. Process Flow Diagram for Lightning StrikePOST CURE PROCEDURESAPPENDIX A - REFERENCESAPPENDIX A - REFERENCES - ContinuedAPPENDIX B - TOOLS AND CONSUMABLE ITEMSAPPENDIX B - TOOLS AND CONSUMABLE ITEMS - ContinuedAPPENDIX B - TOOLS AND CONSUMABLE ITEMS - ContinuedDRILL MOTOR AND DRILL BITSCONSUMABLE MATERIALSTable B-4. - Consumable Materials Table B-4. - Consumable Materials - ContinuedTable B-5. - Vacuum Bagging MaterialsTable B-5. - Vacuum Bagging Materials - ContinuedTable B-6. - Personal Protective Equipment
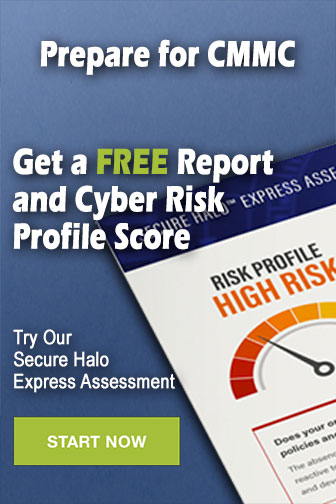